如何提高PC/ABS電鍍性能
電鍍PC/ABS制件以其靚麗的金屬外觀效果,在汽車、家電及IT行業被廣泛使用。材料配方設計和電鍍工藝通常是人們認為影響PC/ABS電鍍性能的主要因素,然而很少有人關注注塑加工工藝對電鍍性能的影響。本文主要從注塑加工工藝對PC/ABS電鍍性能的影響方面進行分析,希望可以對讀者有一些參考作用。
注塑溫度:在材料不會裂解的情況下,較高的注塑溫度可以得到更好的電鍍性能。在較低的注塑溫度下,PC/ABS材料的流動性差,注塑出的產品有較大的內應力,在粗化過程中應力釋放,導致產品表面的刻蝕不均勻,進而導致電鍍產品外觀不良,以及電鍍結合力差的狀況產生。而較高的注塑溫度,可以降低產品的注塑殘留內應力,從而提高材料的電鍍性能。相關研究表明,相較于注塑溫度為230℃的產品,溫度提高到260℃-270℃時,鍍層結合力提高約50%,同時表面外觀不良率也大大降低。然而,注塑溫度也不能過高,如果過了材料的裂解溫度,將會導致注塑產品表面的外觀不良,進而影響其電鍍性能。
注塑速度和壓力:較低的注塑壓力和適當的注塑速度有利于提高PC/ABS的電鍍性能.注塑壓力過大,將導致產品內部分子的過分擠壓,產生較高的產品內應力,進而導致產品粗化不均及電鍍結合力較差;適當提高注塑速度,可以使澆口位置的剪切加大,導致流體溫度的提高,進而會提高整個材料的流動性,有利于產品的充填,降低產品的內應力;但剪切太大會導致材料的裂解,產生氣痕,起皮,毛邊等問題。
保壓壓力及保壓切換點:過高的保壓壓力和較晚的保壓切換位置,導致產品的過度填充和澆口位置的應力集中及產品內部較高的殘留應力。因此要結合實際產品充填狀態來設定保壓壓力和保壓切換點。
模具溫度:高模溫有利于提高材料的電鍍性能。在低模溫狀態下,材料流動性差,產品在充填過程中由于分子之間的擠壓及拉伸,導致產品在冷卻下來后材料的分子鏈取向嚴重,產品成型內應力較大,電鍍性能差;反之在高模溫狀態下,材料流動性好,有利于充填,分子鏈處于自然卷曲狀態,產品內應力小,電鍍性能得到很大提升。實際的模具溫度設定需要結合模具水路,加熱方式以及成型周期的要求來設定,在不影響其它性能的前提下,模具溫度盡量提高;控制模具溫度的同時,也要維持模具溫度的均勻分布,不均勻的模具溫度分布,會導致不均一的收縮內應力進而影響電鍍性能。
螺桿轉速:較低的螺桿轉速有利于提高材料的電鍍性能.螺桿轉速之設定是控制塑料之計量時間,亦即塑料進入料管接受螺桿混練,輸送至噴嘴之時間。螺桿轉速亦同時影響塑化的均勻性,太的螺桿轉速會使螺桿內材料剪切加重,熔體溫度急劇升高,而且螺桿之轉速愈,塑料的混練效果愈差,形成熔膠溫度差異加大,使得充填流動及冷卻亦造成差異,這是產品內應力形成的主要原因之一。因此一般來說,在材料熔融的前提下,螺桿轉速設定在使計量時間稍短于冷卻時間即可。注塑工藝中注塑溫度、注塑速度和壓力、模具溫度、保壓、螺桿轉速等均會對PC/ABS的電鍍性能產生影響。而直接的不良影響就是過高的產品內應力,內應力過大會影響到電鍍粗化階段的刻蝕的均勻性,進而影響到終產品的電鍍結合力。總之,要結合產品結構、模具狀態及成型機臺的狀態,通過設定合適的注塑工藝,設法降低材料的內應力,可明顯提高PC/ABS材料的電鍍性能。
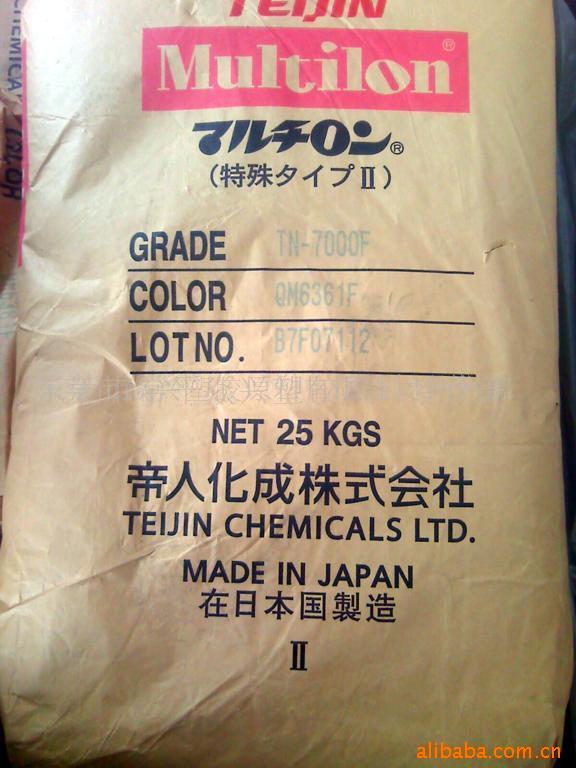
PC/ABS塑膠原料具有PC和ABS兩者的綜合特性。例如ABS的易加工特性和PC的優良機械特性和熱穩定性。二者的比率將影響PC/ABS材料的熱穩定性。PC/ABS這種混合材料還顯示了優異的流動特性。收縮率在0.5%左右。
PC/ABS塑膠原料是一種通過混煉后合成的改性工程塑料。其中,PC就是聚碳酸脂,ABS就是丙烯腈(A)、丁二烯(B)和苯乙 烯(S)的共聚物。這種改性塑料比單純的PC和ABS性能更好,例如:抗沖擊性提高,耐熱性提高,硬度提高等等。ABS塑料 。
PC/ABS樹脂,聚碳酸酯和丙烯腈-丁二烯-苯乙烯共聚物和混合物,是由聚碳酸酯(Polycarbonate)和聚丙烯腈(ABS)合金而成的熱可塑性塑膠,結合了兩種材料的優異特性,ABS材料的成型性和PC的機械性、沖擊強度和耐溫、抗紫外線(UV)等性質,可廣泛使用在汽車內部零件、事務機器、通信器材、家電用品及照明設備上。
注塑工藝
干燥處理:加工前的干燥處理是必須的。濕度應小于0.04%,建議干燥條件為90~110C,2~4小時。
熔化溫度: 230~300C。
模具溫度:50~100C。
注射壓力:取決于塑件。
注射速度:盡可能地高。
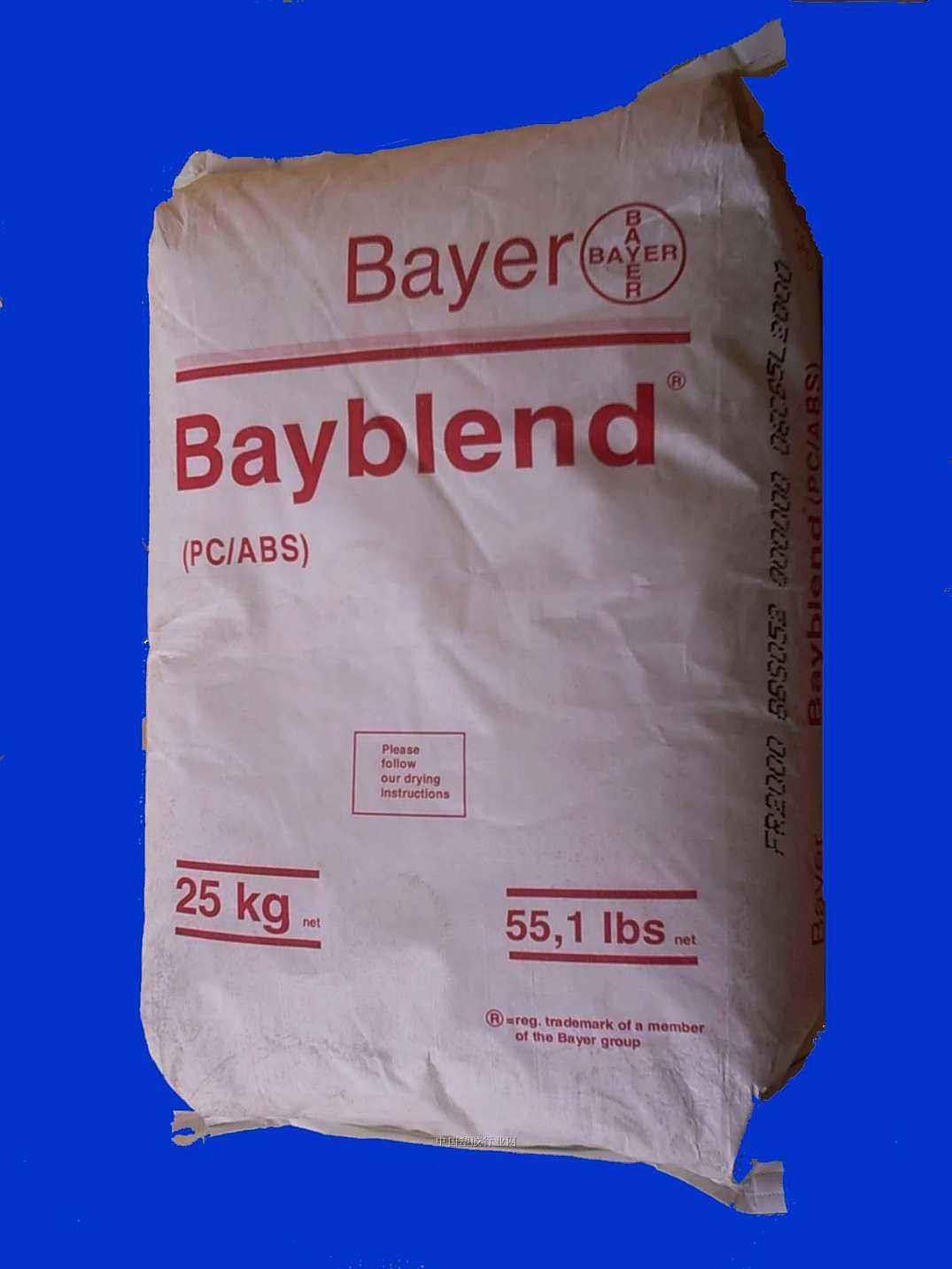
耐水解穩定性PC/ABS:耐水解穩定性系列PC/ABS(HAC8250R)主要應用于汽車儀表板骨架等汽車內飾產品。汽車儀表板骨架作為整個儀表板的支撐結構件,其重要性不言而喻,因此主機廠對儀表板材料提出了更苛刻的要求。目前,儀表板骨架不僅要求有良好的機械性能,加工性能,而且要有的耐水解性能和熱老化性能,以適應汽車在極端高溫,高濕的環境下使用。 新一代耐水解穩定性PC/ABS在PCT(Pressure Cooker Test)測試中,在95%RH,100℃高溫高濕環境1000h后,該PC/ABS中的PC相仍然保持90%以上的分子量,未發生嚴重的水解;而合金的沖擊性能僅下降15%,相比一般PC/ABS提高30%以上的性能。此外,該系列材料為了適應儀表板薄壁化的要求,降低了材料在高剪切下的粘度,克服了過去片面提高溫度來提高材料流動性所帶來的材料熱分解的弊端。 新一代耐水解穩定性PC/ABS材料,由于具有良好的耐水解性和熱穩定性,甚至可以進行回收利用。當添加25%以下的回收料以后,材料的多軸沖擊性能僅下降11%,并且為韌性斷裂,充分顯示了新一代PC/ABS的優越性能。同時該系列材料也經過了大眾實驗室的評測,在80%RH,90℃高溫高濕水解600h后,缺口沖擊強度僅下降8.5%。 目前該材料已經應用在大眾領馭,克萊斯勒300C,通用別克等車型上。
PC/ABS作為世界上銷售量大的商業化聚合物合金,近幾年都以10%左右的需求速度增長。PC/ABS較之PC提高了流動性,改善了加工性能,減少了制品對應力的敏感性,因而廣泛應用于汽車內飾,外飾,車燈等高強度,高耐熱零件。隨著人們環保意識的提高,汽車行業ELV等環保可回收法規的相繼出臺,原材料廠商也不斷提供新的解決方案。作為工程塑料行業的者適時的推出了新一代PC/ABS合金系列材料,它主要包括了耐水解穩定性的PC/ABS,用于免噴涂內飾的低光澤PC/ABS,耐化學品優異不易被油漆等侵蝕的耐化學溶劑PC/ABS等系列產品。
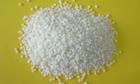
PC/ABS,聚碳酸酯和丙烯腈-丁二烯-苯乙烯共聚物和混合物,是由聚碳酸酯(Polycarbonate)和丙烯腈-丁二烯-苯乙烯共聚物(ABS)合并而成的熱可塑性塑膠,結合了兩種材料的優異特性,ABS材料的成型性和PC的機械性、沖擊強度和耐溫、抗紫外線(UV)等性質,顏色是無透明顆粒,可廣泛使用在汽車內部零件、商務機器、通信器材、家電用品及照明設備上。
PC/ABS,聚碳酸酯和丙烯腈-丁二烯-苯乙烯共聚物和混合物,是由聚碳酸酯(Polycarbonate)和聚丙烯腈(ABS)合并而成的熱可塑性塑膠,結合了兩種材料的優異特性,ABS材料的成型性和PC的機械性、沖擊強度和耐溫、抗紫外線(UV)等性質,可廣泛使用在汽車內部零件、商務機器、通信器材、家電用品及照明設備上。
-/gjdbaj/-
http://www.zhnanke.cc